What does a ‘sustainable’ supply chain look like these days ?
Well in our corner of the world there are two major variants of a sustainable supply chain
- those built for global impact with reporting metrics, incentivising regulations and competition between listed corporates
- those where B2B collaboration, often between small and micro-businesses, build levers for change and provide publics the opportunity to have a say and co-innovate
At Fishy Filaments we have feet in both camps; we’re a micro-business and we effect change through leadership, but we work with corporates and we work in hyper-local collaborations too because as a raw material supplier we can’t make the impact the world needs without customers at all scales.
In this post we’ll look at one specific supply chain step by step and explore what has been achieved to bring abount a higher level of environmental sustainability. We’re going to look at Mutiny Shaving.
Mutiny came to us in 2019 just after our launch of our first 3D printing filament product, Porthcurno.
Their mission is/was to become the world’s most environmentally friendly shaving brand.
As their co-founder Gareth Sturgess says “The business model for Mutiny is to create the most eco friendly shaving products available at the most reasonable prices. We are offering traditional recyclable and reusable products that have been used for years, whilst simultaneously looking to create brand new products in the most eco-friendly new materials and methods to cut out wastes and pollution associated with production and delivery of those items. Cutting edge for a shaving company shouldn’t just mean high performance at the point of delivery next to the skin. It goes all the way back up to the point of conception”.
So there’s a challenge !
Lets go through it step by step.
Material Source – used fishing nets donated by MSC certified Cornish Hake commercial fishing fleet based in Newlyn, Cornwall, UK. These nets would normally be recycled in Slovenia with low to zero local economic benefit and a carbon cost incurred by cross-continental transportation and chemical recycling.
Material recycling by Fishy Filaments Ltd -Local recycling by Fishy Filaments embeds the economic benefit of recycling activity in the local economy and reduces the environmental impact of the recycling itself. The clean nylon that is produced only has 2-3% of the carbon impact vs first use equivalent material.
Material Transfer – The clean nylon recyclate is transferred to Fillamentum in the Czech Republic for extrusion into 3D printing filament. Transportation is carried out under a certified carbon neutral scheme with the couriers, DHL. Fillamentum’s factory operations are partially powered by solar panels.
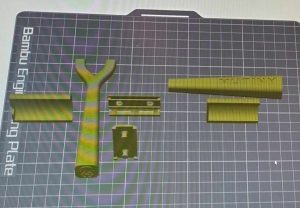
Razor Production – Transportation of the finished filament back to Cornwall is carried out under the same carbon neutral scheme. Production of the razors is carried out on-demand by 3D Printing Cornwall. Very low stocking overhead saves on warehousing and sleeping inventory. Printing is optimised to the material for speed and quality. Any production waste is returned to Fishy Filaments for 3rd gen recycling.
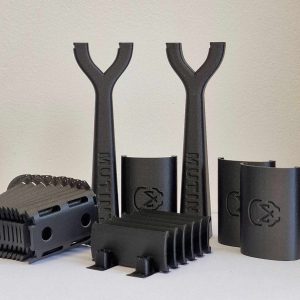
Final distribution and sale – The finished product is sent to Mutiny Shaving in South Wales. The final leg of distribution uses recycled and recyclable packaging so that the only element that is not recycled or recyclable is the razor blade itself, a very small fraction of total product weight.
At every step environmental impact is reduced or removed entirely.
That’s Mutiny Shaving, but we have the same things going with global lighting giant, Signify (Philips Lighting) at the other end of the scale because doing our own little thing just isn’t enough now. Whether changing the global market for shaving equipment or lighting or 3D printing materials demonstration projects are no longer where its at. Deployment at scale is where we need to be.